1 Global Hardfacing Welding Wires Market Size (Value) and CAGR (2024-2033)
In 2024, the global Hardfacing Welding Wires market was valued at USD 425.17 million, with a CAGR of 5.16% from 2024 to 2033.
Hardfacing is the application of hard, wear-resistant material to the surface of a component by welding, thermal spraying, or a similar process, mainly to reduce wear. Hardfacing is used on original equipment as well as for the repair of worn components.
A welding wire is a slender metal material for welding. They will become tools for connecting different materials, which are the materials consumed in the process. Hardfacing welding wires are mainly divided into flux cored and metal cored.
Figure Global Hardfacing Welding Wires Market Size (M USD) and CAGR 2024-2033
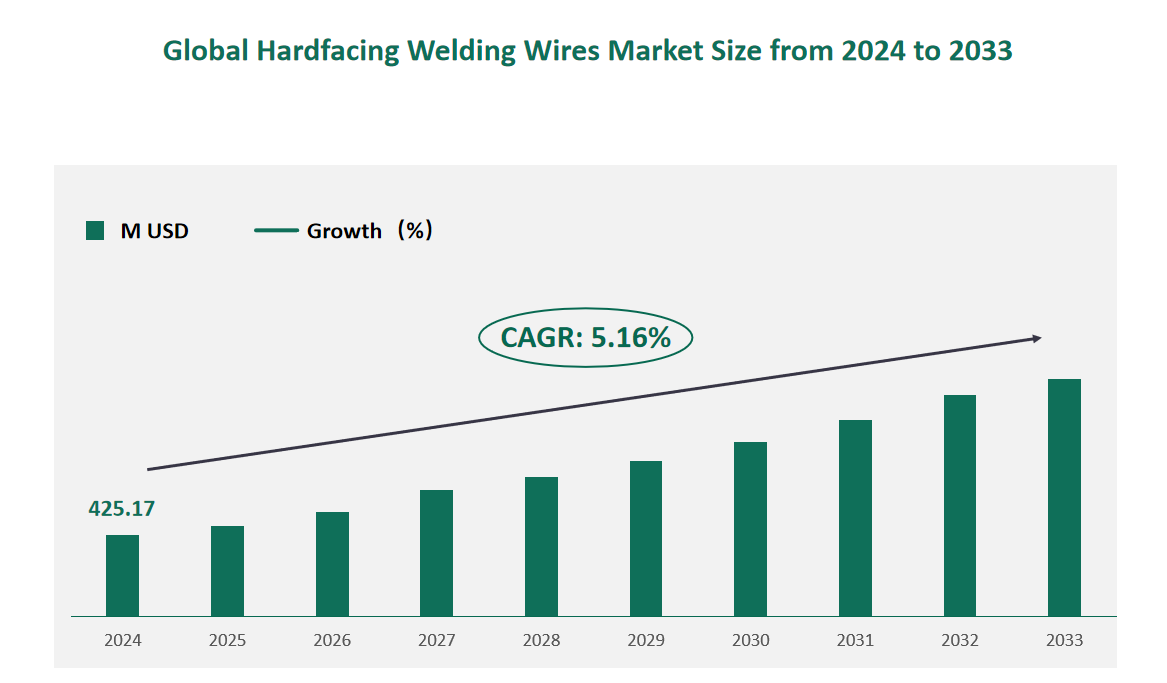
2 Hardfacing Welding Wires Market Drivers
One of the primary drivers is the increasing demand for hardfacing technology in various industrial sectors. Hardfacing is a surface treatment process that significantly improves the wear resistance, heat resistance, and corrosion resistance of components. This technology is widely used in machinery manufacturing, metallurgy, electric power, mining, construction, and petrochemical industries, driving the demand for Hardfacing Welding Wires.
Another significant driver is the development of flux-cored wires, which offer several advantages over traditional welding methods. Flux-cored wires have high welding efficiency, ease of operation, and the ability to produce high alloy and high hardness materials. They are also more adaptable to medium and small batch production, making them a preferred choice for many industrial applications. The utilization rate of flux-cored wires is higher compared to other methods, and they can achieve faster hardfacing speeds, further enhancing productivity.
The market is also positively impacted by the continuous innovation in hardfacing welding wire technology. Suppliers are constantly developing new ideas and technologies to keep pace with advanced industry standards. This innovation is crucial for maintaining competitiveness in a highly competitive market. The ability to easily adjust the composition and properties of flux-cored wires makes them highly adaptable to various metal materials, especially for hardfacing welding materials with high carbon and high alloy content.
3 Hardfacing Welding Wires Market Restraints
Despite the promising growth prospects, the Hardfacing Welding Wires market faces several challenges that can impact its development and expansion. One of the primary challenges is the high cost of raw materials. The prices of raw materials and commodities can fluctuate sharply, leading to increased production costs. This can be particularly problematic when manufacturers are unable to fully pass on these increased costs to their customers, thereby affecting their gross profit margins.
Another significant challenge is the need for proper maintenance of welding equipment. Hardfacing welding wires are susceptible to high temperatures, and if the temperature exceeds their tolerance levels, their efficiency can be compromised. This can lead to cracks and other defects, reducing the lifespan of the wires. Therefore, regular maintenance and timely cooling care are essential to ensure the longevity and effectiveness of the welding wires.
The market also faces intense competition, particularly due to the low-price strategies adopted by some manufacturers. With the rise of e-commerce, product information has become more transparent, leading to increased price sensitivity among consumers. This has resulted in a trend of low-price competition, where companies often engage in price wars to capture market share. This can be detrimental to small and medium-sized enterprises with limited financial resources, potentially leading to their elimination from the market.
4 Global Hardfacing Welding Wires Market Consumption (K Tons) by Type in 2024
Flux Cored Welding Wires are a significant segment of the Hardfacing Welding Wires market. These wires are filled with deoxidizers and alloy compounds, making them highly effective for hardening uneven surfaces. They offer several advantages, including high welding efficiency, ease of operation, and the ability to produce high alloy and high hardness materials. In 2024, the consumption of Flux Cored Welding Wires is projected to be 58.9 K Tons. This type of wire is particularly popular in industries such as metalworking, shipbuilding, and mining due to its superior wear resistance and ability to operate under extreme temperature conditions.
Metal Cored Welding Wires represent another crucial segment of the market. These wires are hollow metal tubes filled with minerals, metals, and chemical powders, often containing a significant amount of iron for enhanced resistance. Metal Cored Wires are known for their high-temperature resistance, superior shock absorption, and reduced corrosive properties. In 2024, the consumption of Metal Cored Welding Wires is expected to reach 31.3 K Tons. This type is widely used in applications requiring high durability and resistance to harsh conditions, such as heavy machinery manufacturing and industrial construction.
Table Global Hardfacing Welding Wires Market Consumption (K Tons) by Type in 2024
Type | Market Consumption (K Tons) 2024 | Market Share 2024 |
Flux Cored | 58.9 | 65.29% |
Metal Cored | 31.3 | 34.71% |
5 Global Hardfacing Welding Wires Market Consumption (K Tons) by Application in 2024
Metalworking is one of the largest applications for Hardfacing Welding Wires. In 2024, the consumption of Hardfacing Welding Wires in the metalworking sector is projected to be 37.1 K Tons. This application benefits from the wear-resistant properties of Hardfacing Welding Wires, which are essential for extending the life of cutting tools, dies, and other metalworking equipment. The ability to harden surfaces and reduce friction makes these wires indispensable in this industry.
The shipbuilding industry is another significant consumer of Hardfacing Welding Wires. In 2024, the consumption in this sector is expected to reach 24.0 K Tons. Shipbuilding requires materials that can withstand harsh marine environments and heavy usage. Hardfacing Welding Wires are used to protect critical components such as propellers, hulls, and other structural parts from wear and corrosion, ensuring the longevity and reliability of ships.
The mining industry also relies heavily on Hardfacing Welding Wires. In 2024, the consumption in this sector is projected to be 11.3 K Tons. Mining operations involve heavy machinery that is subjected to extreme conditions, including abrasive materials and high-impact forces. Hardfacing Welding Wires are used to protect and repair mining equipment such as excavators, drills, and crushers, reducing downtime and maintenance costs.
Table Global Hardfacing Welding Wires Market Consumption (K Tons) by Application in 2024
Application | Market Consumption (K Tons) 2024 | Market Share 2024 |
Metalworking | 37.1 | 41.14% |
Shipbuilding | 24.0 | 26.59% |
Mining Industry | 11.3 | 12.52% |
Others | 17.8 | 19.75% |
6 Global Hardfacing Welding Wires Market Size by Region in 2024
The Americas region, including the United States, Canada, and Mexico, is a significant market for Hardfacing Welding Wires. In 2024, the market value in this region is projected to be 107.04 million USD. The United States is the largest consumer in this region, driven by its robust industrial base and demand from sectors such as metalworking and shipbuilding. Canada and Mexico also contribute to the market, with growing demand from their respective industrial sectors.
Europe is another key region for Hardfacing Welding Wires, with a projected market value of 114 million USD in 2024. Countries such as Germany, France, the UK, Italy, and Spain are major consumers. The European market benefits from advanced manufacturing technologies and a strong demand for high-quality welding materials. The region’s focus on precision engineering and heavy industry drives the need for Hardfacing Welding Wires to enhance equipment durability and reduce maintenance costs.
The Asia Pacific region is the largest market for Hardfacing Welding Wires, with a projected value of 194.19 million USD in 2024. China, Japan, South Korea, India, and Australia are the major markets in this region. China leads the region with significant consumption driven by its vast manufacturing and construction industries. Japan and South Korea are also major consumers, with a focus on high-tech manufacturing and shipbuilding. The rapid industrialization and infrastructure development in India and Southeast Asia contribute to the growing demand for Hardfacing Welding Wires in this region.
Figure Global Hardfacing Welding Wires Market Size by Region in 2024
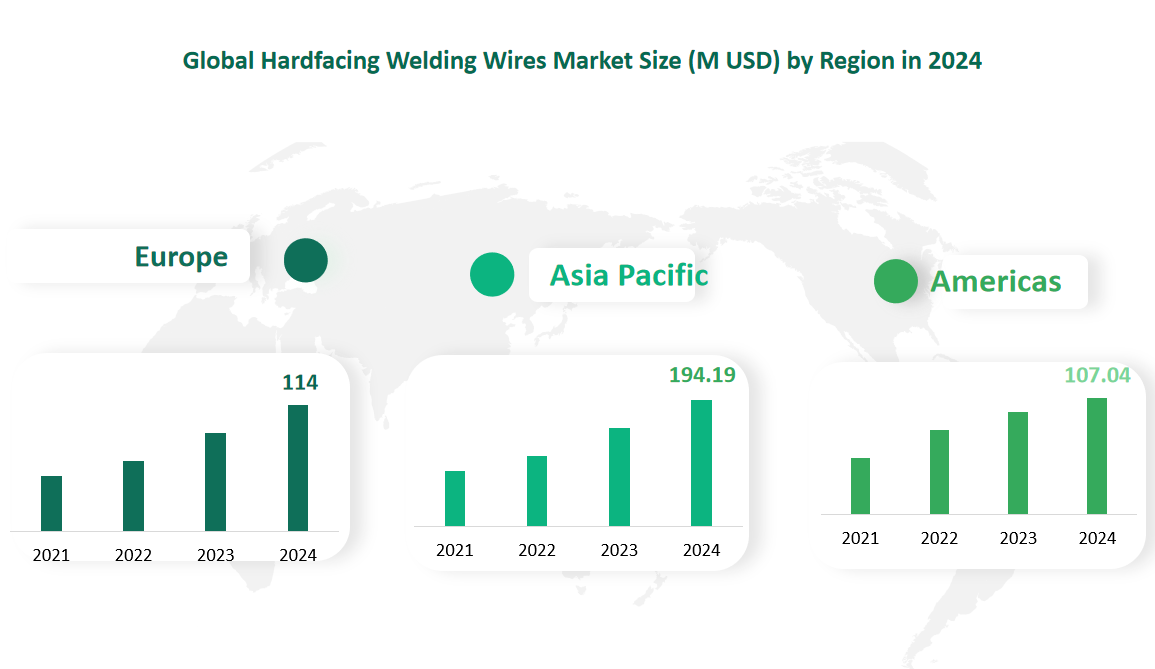
7 Major Players in Global Hardfacing Welding Wires Market
7.1 ESAB
Company Profile:
ESAB is a diversified technology company with a rich history dating back to 1904. Headquartered in Sweden, ESAB has manufacturing plants distributed across America, Europe, and Asia. The company operates globally, offering a wide range of products and solutions in the welding and cutting industry.
Business Overview:
ESAB is a leading provider of orthopedic solutions, industrial welding and cutting products, and special gas regulation and control systems. The company’s main areas of focus include engineering, medical equipment, manufacturing, orthopedics, continuous improvement, and welding and cutting. ESAB’s commitment to innovation and quality has earned it a reputation as a trusted leader in the industry.
Type Introduction:
ESAB offers a variety of Hardfacing Welding Wires, including Stoodite 21-S and Stoody 103CP. Stoodite 21-S is known for its excellent high-temperature strength, galling, cavitation erosion, and corrosion resistance. Stoody 103CP is a submerged arc wire used primarily on coal pulverizer rings and rolls, offering fine relief check patterns that reduce distortion.
Recent Financial Performance:
In the most recent year, ESAB reported a production of 16.1 K Tons of Hardfacing Welding Wires. The company’s revenue reached 97.63 million USD, with a gross margin of 26.26%.
7.2 Hobart Brothers
Company Profile:
Hobart Brothers, established in 1917, is a leading manufacturer of filler metals, including tubular wires (flux-cored and metal-cored), solid wires, and stick electrodes. The company is headquartered in the USA and operates primarily in the North American market, with a global sales reach.
Business Overview:
Hobart Brothers is renowned for its commitment to improving weld quality, increasing productivity, and lowering costs. The company offers a wide range of solutions under the Hobart® brand, focusing on providing high-quality welding materials and equipment. Hobart Brothers’ dedication to innovation and customer satisfaction has solidified its position as a trusted leader in the industry.
Type Introduction:
Hobart Brothers offers several types of Hardfacing Welding Wires, including Tube-Alloy® Build UP-O, Tube-Alloy® 218-O, and Tube-Alloy® AP-O. These wires are designed for specific applications such as build-up on mild and low alloy steels, work hardening austenitic manganese steel alloys, and chromium-manganese austenitic stainless steel alloys. They are used in industries such as bucket teeth and lips, coupling boxes, crane wheels, and crusher jaws.
Recent Financial Performance:
In the most recent year, Hobart Brothers reported a production of 5.4 K Tons of Hardfacing Welding Wires. The company’s revenue reached 32.39 million USD, with a gross margin of 24.45%.
7.3 WALDUN
Company Profile:
WALDUN, established in 2005, is a leading provider of wear solutions, including wear plates, wearing parts, and automatic welding and cutting equipment. The company is headquartered in China and operates globally, offering a wide range of high-quality products and services.
Business Overview:
WALDUN specializes in providing comprehensive wear solutions, leveraging its extensive experience and knowledge in the field. The company’s focus on innovation and customer satisfaction has enabled it to establish a strong presence in the global market. WALDUN’s commitment to quality and reliability has earned it a reputation as a trusted partner for various industries.
Type Introduction:
WALDUN offers a variety of Hardfacing Welding Wires, including the a.035 welding wire. This wire is designed for wear resistance and contains low carbon deposits. WALDUN’s welding wires are carefully studied and manufactured to meet the specific needs of different applications, ensuring high performance and durability.
Recent Financial Performance:
In the most recent year, WALDUN reported a production of 5.4 K Tons of Hardfacing Welding Wires. The company’s revenue reached 13.75 million USD, with a gross margin of 24.60%.