1 Global Flux Cored Welding Wire Market Size (Value) and CAGR (2024-2033)
In 2024, the global Flux Cored Welding Wire market was valued at USD 2167.03 million, with a CAGR of 4.56% from 2024 to 2033.
Flux Cored Welding Wire is a specialized welding material designed for high-efficiency and high-quality welding processes. It consists of a metal sheath filled with flux, which provides shielding and slag protection during welding. This type of welding wire is particularly advantageous due to its ability to deliver high deposition rates, excellent arc stability, and reduced spatter. It is widely used in industries such as shipbuilding, structural fabrication, bridge construction, and machinery manufacturing.
Figure Global Flux Cored Welding Wire Market Size (M USD) and CAGR 2024-2033
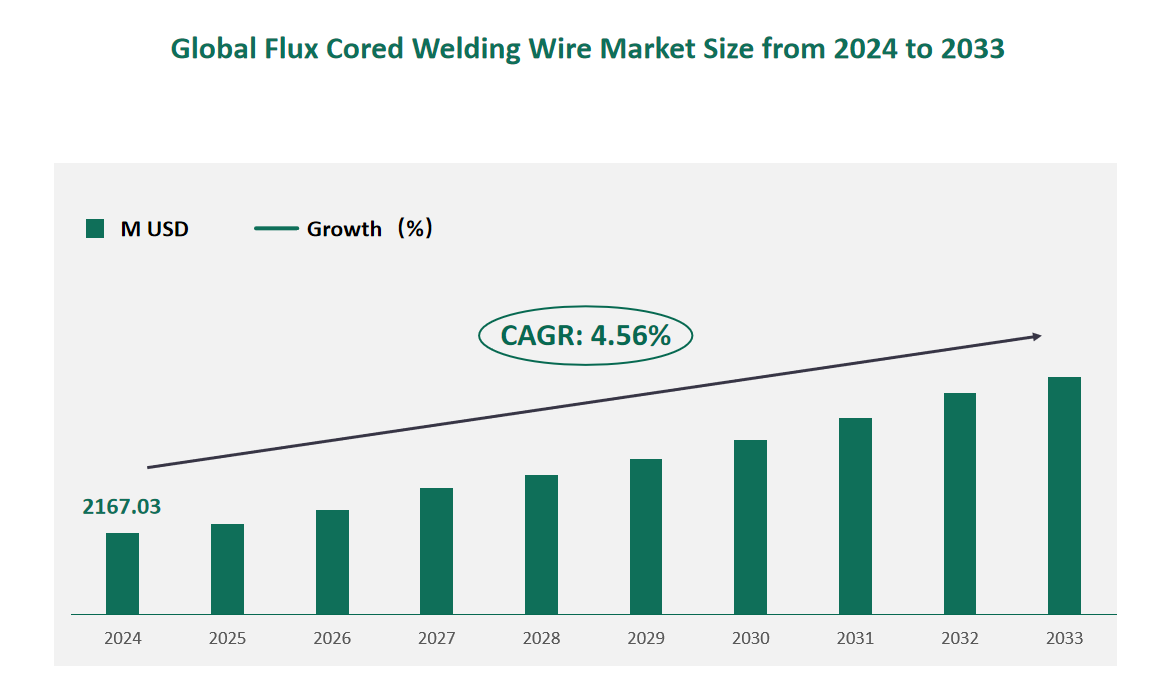
2 Flux Cored Welding Wire Market Drivers
One of the primary drivers of the Flux Cored Welding Wire market is the accelerated pace of infrastructure construction globally. Large-scale projects such as housing developments, transportation networks, and industrial facilities require significant amounts of welding materials. Flux Cored Welding Wire, with its high deposition rates and excellent weld quality, is particularly suited for these applications. Its ability to reduce welding time and improve overall efficiency makes it an essential material in the construction of bridges, steel structures, and heavy machinery.
The welding industry is increasingly adopting advanced technologies and automation to improve efficiency and reduce labor costs. Flux Cored Welding Wire is well-suited for automated and semi-automated welding processes, which are becoming more prevalent in modern manufacturing. Its compatibility with robotic welding systems and other automated equipment allows for consistent and high-quality welds, further enhancing its appeal in industries such as automotive, shipbuilding, and machinery manufacturing.
Flux Cored Welding Wire offers several technical and economic advantages over traditional welding methods. It provides higher welding efficiency due to its continuous welding capabilities and reduced spatter, which minimizes post-weld cleaning and grinding time. Additionally, the wire’s ability to adapt to various steel types and welding positions makes it a versatile solution for different industrial applications. While the initial cost of Flux Cored Welding Wire may be higher than some alternatives, its overall cost-effectiveness is evident in large-scale operations where productivity and quality are paramount.
3 Flux Cored Welding Wire Market Restraints
The Flux Cored Welding Wire market is highly competitive, with numerous manufacturers vying for market share. This competition has led to price wars, as companies attempt to undercut each other to gain a competitive edge. The result is a downward pressure on prices, which can reduce profit margins for manufacturers. Additionally, the market is characterized by product homogenization, making it difficult for companies to differentiate their products and justify higher prices. This intense competition can lead to a “race to the bottom,” where companies prioritize cost-cutting over product quality and innovation.
The cost of raw materials is a significant factor in the production of Flux Cored Welding Wire. Fluctuations in the prices of steel, iron ore, and other key inputs can impact production costs and profitability. In recent years, the market has experienced volatility in raw material prices, driven by factors such as supply chain disruptions, geopolitical tensions, and changes in global demand. Manufacturers must carefully manage their procurement strategies to mitigate the impact of these price fluctuations, but this can be challenging in a dynamic market environment.
4 Global Flux Cored Welding Wire Market Size by Type in 2024
Seamed Tubular Welding Wires are manufactured by taking a U-shaped strip of metal, filling it with a powdered core material, and then rolling and sealing it into a thin wire. This type of welding wire is known for its versatility and cost-effectiveness. In 2024, the market value for Seamed Tubular Welding Wires was 1,233.04 million USD.
Seamless Tubular Welding Wires are manufactured by pouring the core material into a seamless pipe band. This process eliminates the seam, resulting in a smoother and more consistent wire. In 2024, the market value for Seamless Tubular Welding Wires was 993.20 million USD.
Table Global Flux Cored Welding Wire Market Size by Type in 2024
Type | Market Size (M USD) 2024 |
Seamed tubular welding wires | 1202.64 |
Seamless tubular welding wires | 964.40 |
5 Global Flux Cored Welding Wire Market Consumption (K Tons) by Application in 2024
In 2024, the global consumption of Flux Cored Welding Wire was segmented across several key applications, each contributing to the overall market demand. Shipbuilding remained the dominant application, consuming a substantial portion of the market. Specifically, 1651.2 K Tons were used in shipbuilding. This high demand is attributed to the industry’s need for high-strength, durable welding materials capable of withstanding harsh marine environments.
Structural fabrication also played a significant role, with 88.3 K Tons consumed in 2024. This application includes the construction of steel bridges, buildings, and other large-scale structures, where Flux Cored Welding Wire is valued for its ability to provide strong, reliable welds in various positions.
Bridges accounted for 66.6 K Tons of consumption. The use of Flux Cored Welding Wire in bridge construction is driven by its excellent mechanical properties and resistance to environmental factors, ensuring long-term durability and safety.
Table Global Flux Cored Welding Wire Market Consumption (K Tons) by Application in 2024
Application | Market Consumption (K Tons) 2024F | Market Share 2024 |
Machinery | 25.6 | 1.38% |
Structural Fabrication | 88.3 | 4.78% |
Ship Building | 1651.2 | 89.30% |
Bridges | 66.6 | 3.60% |
Others | 17.3 | 0.94% |
6 Global Flux Cored Welding Wire Market Size by Region in 2024
In 2024, North America led the market with a revenue of 547.2 million USD. This region’s dominance is driven by its advanced manufacturing industries, particularly in shipbuilding and heavy machinery, which require high-quality welding solutions.
Europe followed closely with a revenue of 419.37 million USD. The region’s robust industrial base, especially in countries like Germany and the UK, supports the demand for Flux Cored Welding Wire in structural fabrication, shipbuilding, and automotive manufacturing. European companies are also at the forefront of technological advancements, contributing to the development of high-performance welding materials.
Asia-Pacific emerged as a significant market, with China and Japan leading the way. China’s market revenue reached 424.63 million USD in 2024. The rapid industrialization and infrastructure development in China have driven the demand for Flux Cored Welding Wire, particularly in shipbuilding and heavy machinery manufacturing. Japan, known for its advanced manufacturing capabilities, contributed $346.03 million USD or 18.2% of the global market, with a focus on high-quality welding solutions for shipbuilding and steel structures.
Figure Global Flux Cored Welding Wire Market Size by Region in 2024
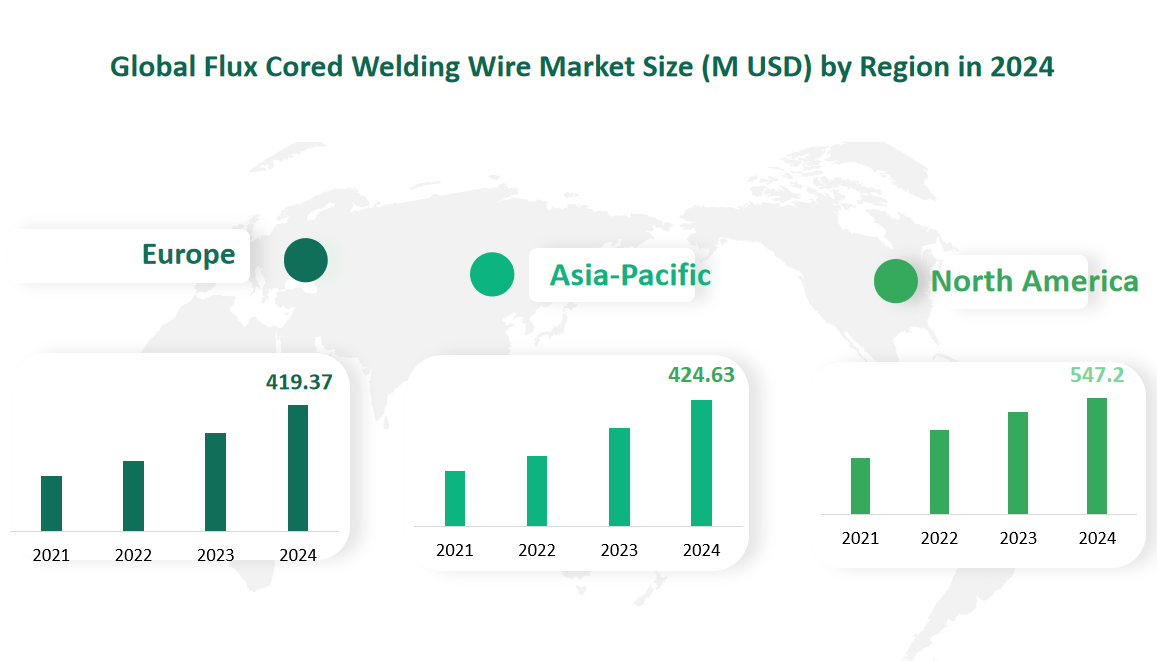
7 Major Players in Global Flux Cored Welding Wire Market
7.1 ITW (Illinois Tool Works Inc.)
Company Profile:
ITW is a leading global manufacturer of engineered fasteners, components, and specialty products. Founded in 1912 and headquartered in Glenview, Illinois, ITW has a strong presence in North America, Europe, and Asia. The company is renowned for its innovative solutions and high-quality products, catering to a wide range of industries, including automotive, aerospace, construction, and shipbuilding. ITW’s business model is built on a decentralized structure, allowing for flexibility and innovation across its various divisions.
Business Overview:
ITW’s business is characterized by its focus on high-quality welding solutions and consumables. The company offers a comprehensive range of Flux Cored Welding Wires, including gas-shielded and self-shielded varieties, designed for various industrial applications. ITW’s products are known for their high deposition rates, excellent arc stability, and superior mechanical properties, making them ideal for shipbuilding, structural fabrication, and heavy machinery manufacturing.
Product Introduction:
One of ITW’s flagship products is the Hobart 811K2 Flux Cored Wire. This all-position wire is designed for use with 100% CO2 shielding gas and provides excellent impact properties down to -60°C. It is widely used in offshore structures, LNG and LPG carriers, and storage tanks. The wire’s fast-freezing slag system ensures high deposition rates and a smooth welding process, making it a preferred choice for demanding applications.
Recent Financial Performance:
In the most recent year, ITW reported a production volume of 152.9 K Tons of Flux Cored Welding Wire, with a revenue of 220.57 million USD.
7.2 ESAB (Electric Steel Apparatus and Boiler)
Company Profile:
ESAB is a diversified technology company with a long history dating back to 1904. Headquartered in Annapolis Junction, Maryland, ESAB operates manufacturing plants across North America, Europe, and Asia. The company is a global leader in welding and cutting solutions, offering a wide range of products and services, including Flux Cored Welding Wires, welding equipment, and consumables. ESAB’s commitment to innovation and quality has earned it a strong reputation in the industry.
Business Overview:
ESAB’s business is centered around providing advanced welding and cutting solutions for various industries, including automotive, shipbuilding, construction, and heavy machinery. The company’s Flux Cored Welding Wires are known for their high performance, versatility, and reliability. ESAB’s product portfolio includes both gas-shielded and self-shielded wires, designed to meet the specific needs of different applications.
Product Introduction:
ESAB’s CRYO-SHIELD NI9 Flux Cored Wire is a gas-shielded wire designed for welding 9% nickel steel. This wire is used for welding in all positions with 100% CO2 shielding gas and offers excellent crack resistance and anti-porosity properties. It is widely used in the shipbuilding and offshore industries, where high toughness and low-temperature performance are critical.
Recent Financial Performance:
In the most recent year, ESAB reported a production volume of 110.8 K Tons of Flux Cored Welding Wire, with a revenue of 151.94 million USD.
7.3 Lincoln Electric
Company Profile:
Lincoln Electric, founded in 1895, is a global leader in the design, development, and manufacture of arc welding products, robotic welding systems, plasma and oxyfuel cutting equipment, and brazing and soldering alloys. Headquartered in Cleveland, Ohio, Lincoln Electric operates manufacturing facilities across North America, Europe, and Asia. The company is renowned for its high-quality products and innovative solutions, catering to a wide range of industries, including shipbuilding, construction, and heavy machinery.
Business Overview:
Lincoln Electric’s business is characterized by its focus on providing comprehensive welding solutions. The company offers a wide range of Flux Cored Welding Wires, including gas-shielded and self-shielded varieties, designed for various industrial applications. Lincoln Electric’s products are known for their high deposition rates, excellent arc stability, and superior mechanical properties, making them ideal for shipbuilding, structural fabrication, and heavy machinery manufacturing.
Product Introduction:
One of Lincoln Electric’s flagship products is the UltraCore® HD-C Flux Cored Wire. This mild steel, gas-shielded wire is designed for the shipbuilding industry, providing high deposition rates and a flat bead appearance. The wire’s fast-freezing slag system ensures high deposition rates and a smooth welding process, making it a preferred choice for demanding applications.
Recent Financial Performance:
In the most recent year, Lincoln Electric reported a production volume of 96.3 K Tons of Flux Cored Welding Wire, with a revenue of 141.98 million USD.